Overview
The injection molding industry has seen the utilization of various process-monitoring systems over time. Initially, these systems primarily focused on tallying the produced parts, serving as an accounting tool.
However, we made a forward-looking choice two decades ago by adopting Shotscope – not only to monitor but also to regulate the molding process. This strategic decision marked a significant technical advancement for our company, enhancing our grasp of injection molding science.
1. Real-Time Process Control
Shotscope meticulously oversees each individual process parameter (input), constituting authentic process control, as it focuses upstream rather than merely on the aftermath of those parameters. In-cavity sensing techniques (e.g., RJG, Kistler, etc.), on the other hand, observe the resulting output of the amalgamated process parameter settings.
When a process undergoes variation, Shotscope pinpoints the precise, altered parameter. To illustrate the distinction, consider this scenario: If an in-cavity sensor detects temperature changes, what’s the underlying cause?
It might stem from a defective heater band, alterations in injection speed, modifications in screw recovery speed or shifts in mold temperature.
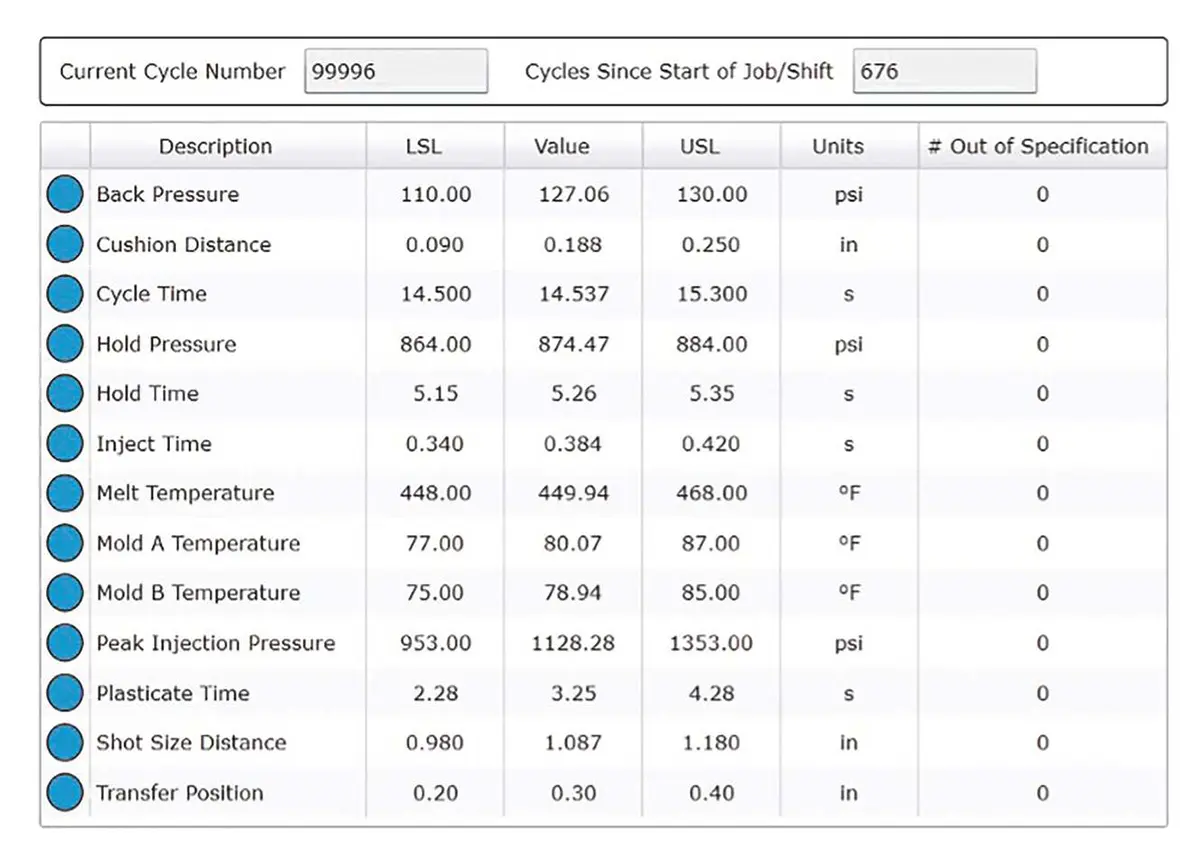
2. Process Development
Through Shotscope, we gain the ability to define the molding process comprehensively and establish the statistical boundaries for each molding process parameter. By comprehending the statistical distribution of each parameter, we gather essential data for the purpose of process qualification and validation. Rigorously testing the cumulative limits and demonstrating the adherence of molded products to specifications within these limits furnishes us with a substantial advantage, resulting in a robust validation protocol.
Our distinctive validation approach empowers us to assess all molding parameters at their utmost limits – high, low or nominal. This method effectively curtails the number of molding trials required, all while preserving the integrity of the validation process. Additionally, this practice contributes to reducing customer validation expenditures.
For products of highest significance, a more comprehensive validation protocol might entail Design of Experiments (DOE) to pinpoint the most impactful process parameters and their interplay.
Our expertise also extends to navigating the realm of medical, pharmaceutical and
FDA validation standards.
3. Statistical Process Control
Our dedication to process control is unwavering. Shotscope stands as a valuable instrument for acquiring process data and performing statistical analysis. After meticulous process development, rigorous qualification and comprehensive validation, parameter limits are established through a blend of statistical analysis, industry benchmarks and the depth of Medbio’s experience. Our molding processes consistently operate within these validated limits. Should any parameter veer beyond these boundaries, an alarm is triggered, leading to the automatic separation of the non-conforming product from the acceptable production. Throughout production, we maintain vigilant oversight of the process’s statistical control, with the primary aim of identifying variations before they compromise the adherence of molded products to specifications.
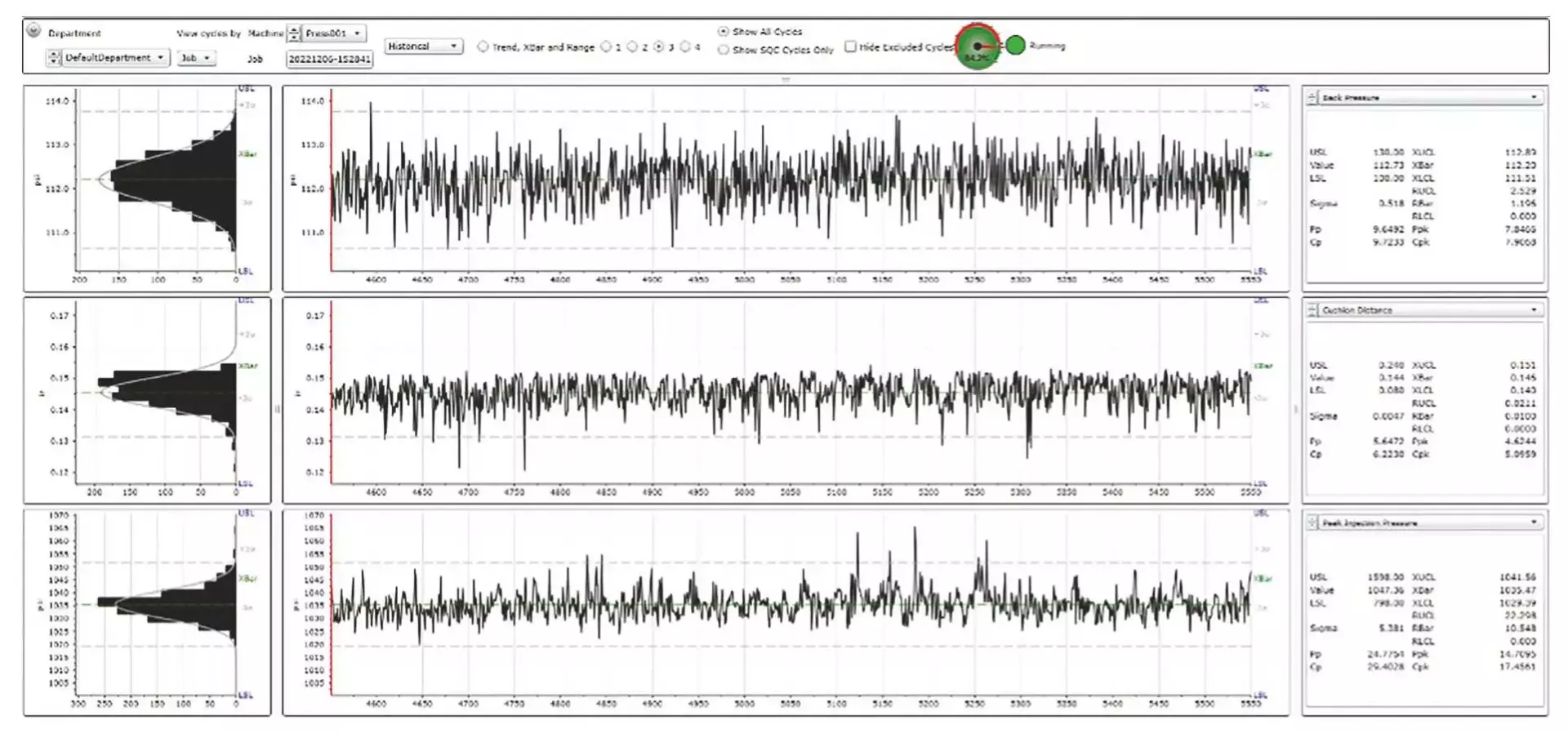
4. Centralized Data Collection
Every process data point finds its home in a centralized system. The sheer volume of data generated through molding processes, coupled with the multitude of process parameters and machinery involved, can be quite overwhelming. Enter Shotscope – an invaluable resource that centralizes the monitoring of all process data, whether from a comprehensive plant level, a machine-specific scale or even at a micro level, parameter by parameter.
This dynamic system ensures process information is readily accessible to our technicians, engineers, schedulers and managers, facilitating informed decision-making.
The depth of our data collection is truly remarkable. From every parameter in every cycle of every molded part. we meticulously archive a comprehensive record.
This means that the complete history of each molded component is safely stored and readily retrievale whenever needed.
5. Quality Control
Product quality control establishes a vital link between molded components and the underlying process, serving as a stringent process audit. Through a combination of part measurement, meticulous inspection and rigorous statistical analysis – augmented by the implementation of statistical process control – we ensure the delivery of flawless products that align perfectly with specifications.
6. Everything Else
Shotscope serves as a versatile tool – not only for production scheduling but also for gauging required preventive maintenance and accurately accounting for parts, run-time, utilization and overall operational efficiencies.
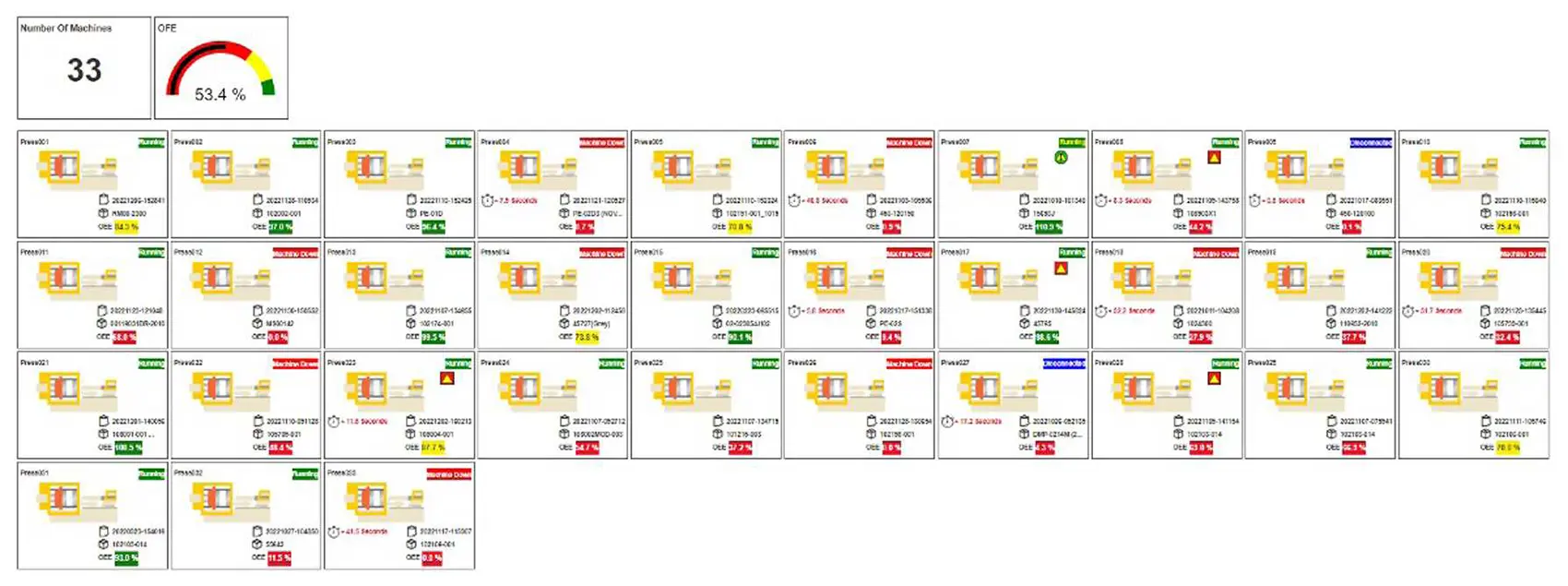
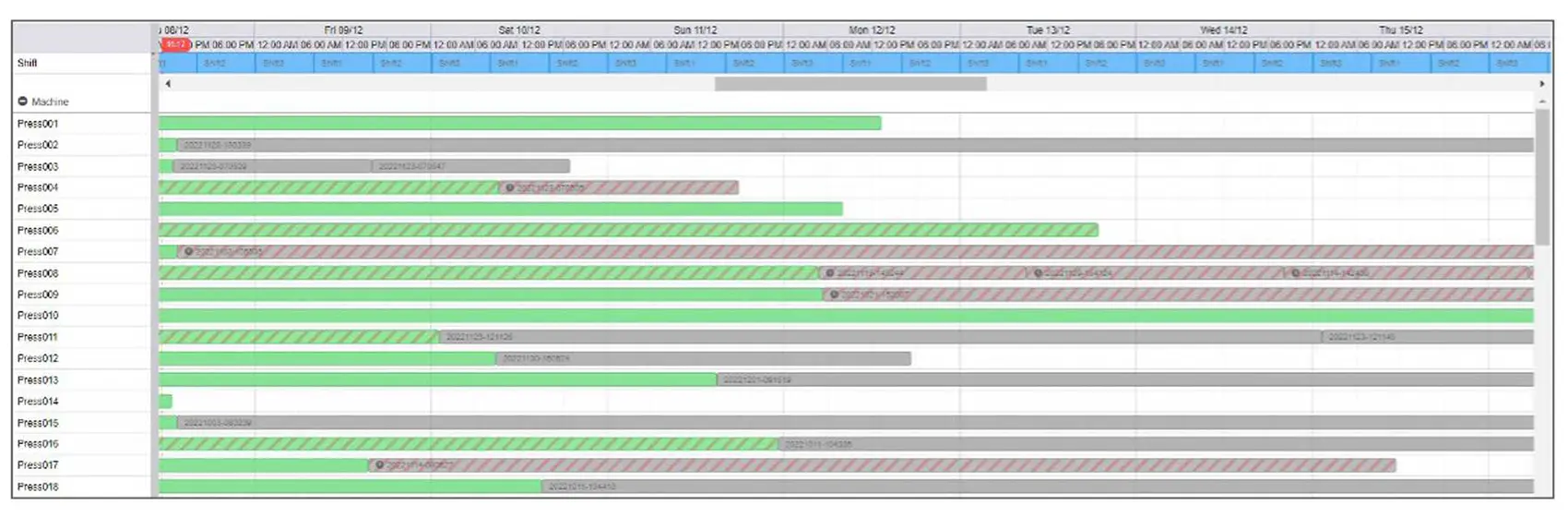
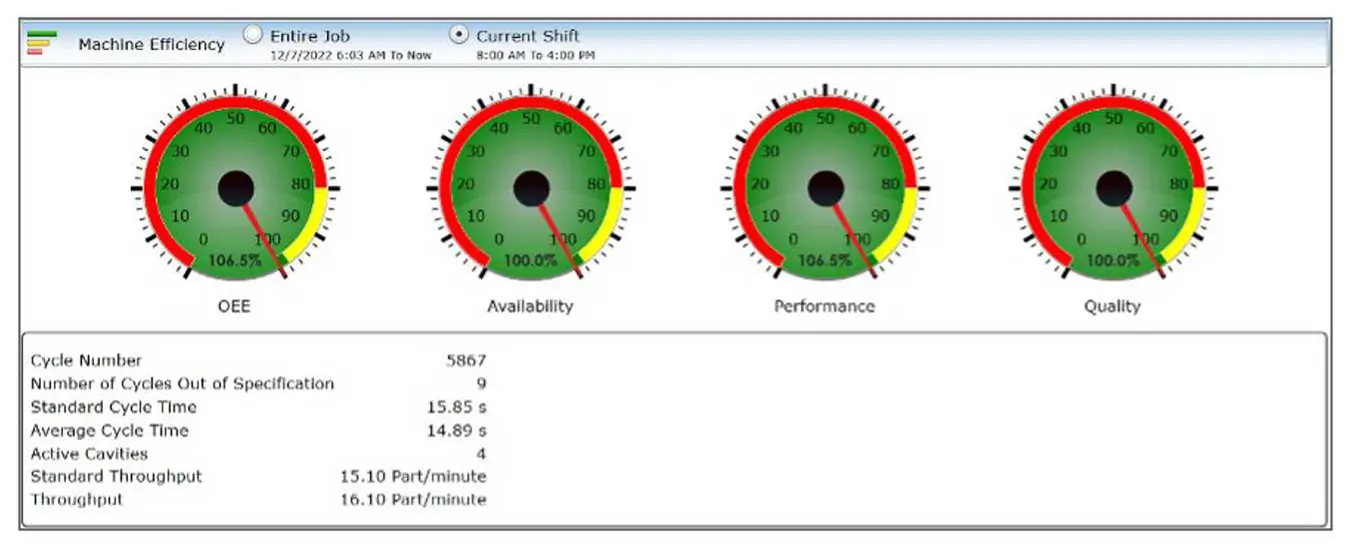